At its core, CNC milling includes the removal of material from a workpiece via a series of collaborated motions. As soon as the layout is finished, the operator uses computer-aided production (CAM) software program to convert the CAD version right into a collection of guidelines that the CNC equipment can read, normally in the kind of G-code.
Among the standout attributes of CNC milling is its adaptability. Unlike standard milling makers, which usually operate along one or two axes, CNC milling devices can operate on numerous axes simultaneously-- commonly three, four, or perhaps five. This capability permits makers to achieve a lot more complex geometries than ever. A three-axis milling device can move along the Z, y, and x axes to create a variety of shapes, while a five-axis device can rotate the workpiece and turn, allowing accessibility to hard angles and surface areas. This adaptability not just improves design possibilities but also streamlines the manufacturing procedure, as it decreases the need for numerous configurations and comprehensive hand-operated interventions.
Explore cnc milling guide the transformative globe of CNC milling, a modern technology that incorporates precision and automation to generate premium elements efficiently from different materials, and find its procedures, advantages, and vital considerations for success in modern-day production.
The option of tools is one more essential facet of CNC milling. The appropriate tool choice can significantly affect the high quality of the completed product and the efficiency of the machining process.
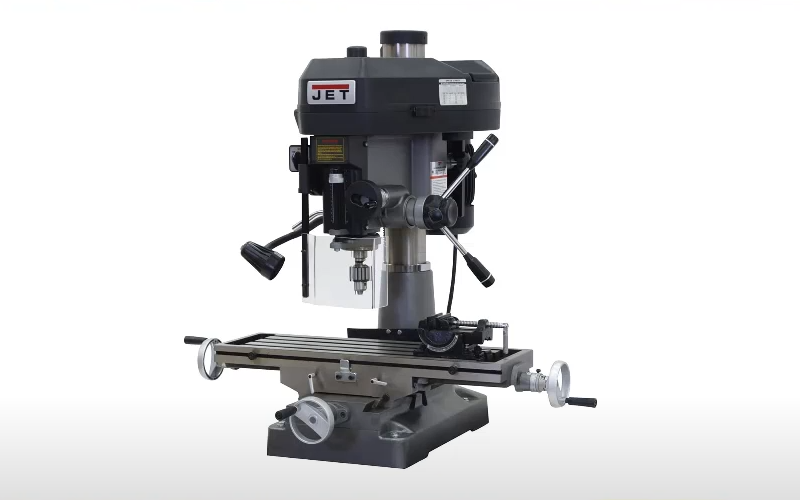
One important variable to consider in CNC milling is material compatibility. Relying on the sort of material being machined, parameters such as reducing speed, feed price, and tool selection might require to be adjusted as necessary. Soft materials like plastics can often be machined at greater rates compared to harder materials like steel, which require slower rates and more durable tooling. Recognizing the buildings of the material, including its firmness, machinability, and thermal conductivity, permits operators to enhance the milling procedure and achieve exceptional outcomes while decreasing wear and tear on tools.
Past the technical factors like design, tooling, and materials, there are additional considerations for maximizing CNC milling procedures. Making use of innovative attributes such as toolpath optimization methods can enhance the milling process further, enabling much faster machining cycles and minimizing waste.
One of the significant benefits of CNC milling is the capability to automate recurring tasks, which decreases human mistake and enhances manufacturing uniformity. While standard milling machines call for a proficient operator to oversee the production procedure, CNC milling devices can run unattended, carrying out pre-programmed instructions with precision. This level of automation not only improves effectiveness yet additionally liberates experienced workers from mundane jobs, permitting them to concentrate on even more useful tasks such as quality assurance and process improvement.
Despite its advantages, transitioning to CNC milling is not without obstacles. Preliminary financial investment can be substantial, with expenses connected with acquiring CNC equipments, software application, and experienced personnel training. Nonetheless, numerous businesses discover that the lasting cost savings related to enhanced performance, reduced product waste, and improved item top quality outweigh the preliminary prices. Additionally, the accessibility of leasing options and budget-friendly entry-level CNC milling makers has made it much more accessible for mid-sized and tiny organizations to embrace this innovation.
Training and skill development for personnel operating CNC milling machines are also essential for taking full advantage of the return on financial investment. Operators need a strong understanding of both the CNC equipment itself and the software application being utilized for programming and monitoring. Several makers find success by providing internal training programs or partnering with external training companies to furnish their teams with the needed skills and understanding.
In recent years, technical developments proceed to shape the area of CNC milling. As markets increasingly transform to automation, integrating attributes such as artificial knowledge (AI) and machine discovering into CNC makers can better improve the accuracy and performance of milling operations.
Additionally, innovations in software are constantly tightening the gap between style and production. Modern CAD/CAM systems currently supply a lot more user-friendly user interfaces and enhanced simulation abilities, enabling drivers to picture machining procedures prior to they are carried out. By detecting potential issues in the design phase, firms can resolve layout problems or enhance cutting techniques without incurring pricey changes to physical products.
In the context of CNC milling, sustainability is likewise obtaining significance as suppliers search for means to reduce their environmental influence. Implementing methods such as maximizing reducing parameters, using a lot more reliable tooling, and recycling materials can add to a much more sustainable milling operation. Furthermore, innovations such as additive production are being checked out in combination with CNC milling, providing chances for hybrid production methods that even more enhance sustainability by minimizing waste.
Explore benchtop milling machine the transformative globe of CNC milling, an innovation that combines accuracy and automation to generate top notch elements successfully from different materials, and find its processes, benefits, and key factors to consider for success in modern production.
In final thought, CNC milling represents a necessary possession in modern-day manufacturing, supplying companies with the capability to produce complicated and high-grade components successfully. Understanding CNC milling begins with a strong structure in its procedures, including the interplay between style, tooling, products, and software program. Ultimately, successful combination of CNC milling machinery, proficient labor force training, and clever automation leads the means for the future of production, where top quality, performance, and sustainability become the hallmarks of functional excellence.